STORIES IN THE MAKING
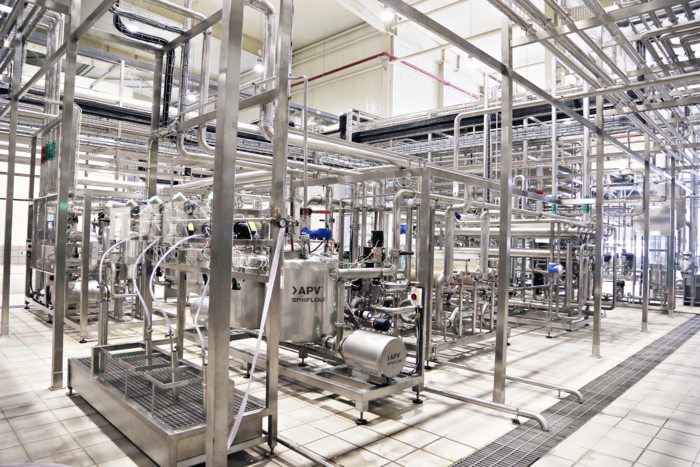
SPX FLOW First Year Care Program
Seamless Equipment Integration: Why the First Year Matters
Investing in new process equipment can be a transformative step for any manufacturing operation. It represents a commitment to innovation and improvement—whether to boost efficiency, meet rising demand or improve product quality, these changes represent a significant commitment of time, money and strategic focus. But successful equipment integration isn’t just about acquisition and installation; it’s about what happens next.
The first year is a critical window—a time when processes are established, teams are established and trained and the foundations for long-term performance are laid. Unfortunately, it’s also when many manufacturers encounter avoidable challenges such as inefficiencies, unplanned downtime and a lack of operational confidence. The reason? Integrating new equipment into existing operations is complex and the right expertise can make all the difference.
From Installation to Optimization: The First-Year Challenge
It is easy to presume that once new equipment is installed, operations will run smoothly. But installation is just the start. To get the best performance and to maximize return on investment manufacturers need a structured approach that includes hands-on training, proactive maintenance planning and real-time support.
Without this, manufacturers often quickly run into common first-year challenges:
- Unplanned Downtime: New equipment requires new procedures. Without proper training and support, even minor issues can escalate, halting production and impacting profitability.
- Knowledge Gaps: Advanced equipment often comes with a learning curve. Without guidance, teams may struggle to leverage its full potential.
- Operational Inefficiency: Misconfigurations or underutilized features can lead to wasted energy, time and resources—directly impacting margins and competitiveness.
These challenges don’t just affect day-to-day operations—they can impact competitiveness, long-term return on investment and may impact a manufacturer’s ability to stay ahead in an increasingly competitive marketplace.
Why Partnering with Experts Matters
The value of partnering with experts during this critical first year cannot be overstated. Expert support during this first year can help avoid pitfalls and establish a solid foundation for success. It ensures equipment runs as designed, delivers the expected outcomes and empowers teams to manage it effectively over the long term.
Key areas where expert support adds value include:
Efficient Start-up:Transition smoothly from installation to production with minimal disruption.
- Proactive Maintenance: Identify and address potential issues through scheduled checks and ongoing monitoring.
- Team Empowerment: Provide practical training that builds confidence and helps teams respond effectively to manage, maintain and optimize the new equipment.
- Performance Monitoring: Use data to evaluate system performance and uncover opportunities for further optimization.
Ultimately, expert support is not just about troubleshooting; it’s about transformation. It is helping manufacturers unlock the full potential of their equipment investment, right from the start.
Supporting You Every Step of the Way
At SPX FLOW, we understand the importance of this first year. That’s why we offer our First Year Care Program—a comprehensive support package designed to help manufacturers achieve operational excellence from day one. From essential spare parts and 24/7 remote support to comprehensive training and performance audits, we’re here to ensure you have the resources and guidance you need during this pivotal period.
Our goal is simple: to help you transition smoothly, operate confidently and achieve long-term success. It’s a flexible, high-impact way to ensure your team is prepared, your equipment is optimized, and your investment pays off—right from the start.
Learn more about how SPX FLOW’s First Year Care Program can help you unlock the full potential of your equipment investment.