Products
- Analyzers
- Automation Systems
- Butter Equipment
- Centrifuges
- Cleaning-in-Place Systems
- Deareators
- Draught Regulators
- Evaporators
- Fat Crystalization Equipment
- Filters & Strainers
- Fluid Bed Dryers
- Heat Exchangers
- Homogenizers
- Membrane Filtration Systems
- Microparticulation Systems
- Mixers & Agitators
- Pasturization Systems
- Pigging Systems
- Plumbing Products
- Pumps
- Recreational Marine Products
- Recreational Marine Pumps
- Spin Flash Dryers
- Spray Dryers
- UHT Systems
- Valves
- Adhesives & Sealants
- Automotive Heating System
- Baby Food
- Bakery Filing Cream
- Beer, Cider, Wine & Spirits
- Biodiesel
- Boats & Watercraft
- Building Infrastructure
- Butter & Spreads
- Cement
- Cheese
- Chocolate
- Coffee & Tea
- Condiments, Sauces & Soups
- Cosmetics
- Dairy Powders
- Ethanol
- Flavors & Fragrances
- Fruit Juice
- Fuel Supply System
- Hair, Nail & Skin Care Products
- Ice Cream
- Inorganic Chemicals
- Margarine & Shortening
- Meat & Animal-Based Proteins
- Milk & Cream
- Neutralization
- Nutraceuticals
- Oral Care
- Paints & Coatings
- Petrochemicals
- Pipelines
- Plant-Based Food & Beverages
- Plastic & Resins
- Refinery
- Soft Drinks
- Solvents & Solutions
- Specialty Chemicals
- Synthetic Rubber
- Yogurt
Plate Heat Exchangers
OVERVIEW
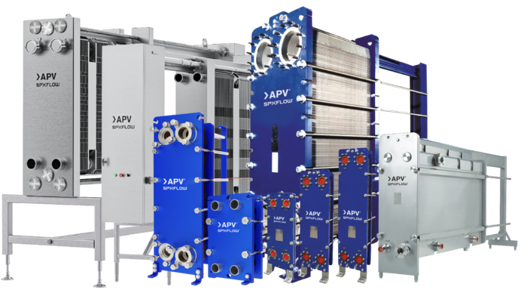
Our plate heat exchangers (PHEs) offer numerous benefits, including high heat transfer efficiency, versatility, easy maintenance, energy efficiency, cost-effectiveness, and safety, making them a popular choice for a wide range of industrial and sanitary applications.
Our solution makers invented the PHE more than a century ago and have continued to collaborate with customers to engineer innovative designs to meet their most challenging needs.
SPARE / REPLACEMENT PARTS
Why Select Genuine Spart Parts for Your Plate Heat Exchanger
Because Downtime is the Enemy of Efficiency
Certain plate heat exchanger replacement parts may seem attractive because of price, but saving on that initial cost could be a costly decision in the long run. There are reasons that alternative, “pirate” parts cost less, including the possible use of lower quality materials or not quite meeting design specifications. This could result in a part not lasting as long, lacking efficiency…or even damaging your equipment. SPX FLOW genuine spare parts are designed to exacting detail: tensile strength, specifications and dimensions are all measured meticulously. Differences in any of these product factors could have a significant effect on the efficiency, yield and health of your industrial machinery.
Why Use Genuine Spare Spares in Your Plate Heat Exchanger
Installing a third-party aftermarket plate in your PHE can lead to inefficiencies that can cost you money. The exact performance characteristics of a genuine APV heat exchanger plate are calculated for your specific application. Every feature of the plate selected by our experienced application engineers is designed to optimize performance. Third-party manufacturers may take shortcuts to minimize upfront expenses, which can hurt performance costing you in the long run. Additionally, a third-party aftermarket plate heat exchanger part into your original plate heat exchanger, will void your plate heat exchanger’s warranty. That’s because all our parts are engineered to our design specifications. Even the smallest of details are considered in the development of our genuine OEM spare parts to not just prevent damage to your equipment, but to also ensure your equipment continues to operate at the highest level of efficiency.
How to Get Genuine Spare / Replacement Plate Heat Exchanger Parts
Our global partner network means the plate heat exchanger replacement parts you need to stay up and running are readily available. And in the event you require expert installation, our partners are fully trained and ready to help at a moment’s notice.
Why Genuine Spare / Replacement Plate Heat Exchanger Parts Are Key
Safety is our top priority at SPX FLOW, which is why all our plate heat exchanger replacement parts endure rigorous testing and comply with regulatory requirements including 3-A and ASME standards. This commitment to safety translates to plate heat exchanger spare parts we stand behind. Can the same be said for third-party replacement parts?
No amount of downtime and certainly no potential safety hazard is worth saving a few bucks on a “might fit” part in the short term.
Don’t take unnecessary risk. Order genuine OEM plate heat exchanger replacement parts today, and rest assured you made the right decision.
FREQUENTLY ASKED PLATE HEAT EXCHANGER QUESTIONS
Plate heat exchangers are a type of heat transfer device that use stacked plates to transfer heat between a product and a media without them coming into direct contact. They are widely used in various industries and applications due to their numerous benefits, which include: High Heat Transfer Efficiency: Plate heat exchangers are designed with large surface areas and thin plates, which promote efficient heat transfer between the the product and the media. The turbulent flow created by the corrugated plates helps to maximize heat transfer and reduce fouling, resulting in high overall heat transfer efficiency. Compact Size and Space-saving Design: Plate heat exchangers have a compact design compared to other types of heat exchangers, such as shell-and-tube heat exchangers. This makes them ideal for installations where space is limited. Plate heat exchangers can be easily customized and arranged in various configurations to meet specific application requirements. Versatility and Flexibility: Plate heat exchangers can handle a wide range of fluids, including liquids, gases, and slurries, making them suitable for a wide range of applications. They can be used for heating, cooling, condensing, and evaporation processes, and can operate under different temperature and pressure conditions. Plate heat exchangers can also be easily modified or expanded to accommodate changing process requirements. Easy Maintenance and Cleaning: Plate heat exchangers are designed with removable plates, which makes them easy to clean and maintain. Fouling can be minimized due to proper design and maintenance, which helps to reduce downtime and maintain optimal heat transfer performance. Energy-efficient: Plate heat exchangers promote efficient heat transfer, which can help reduce energy consumption in heating and cooling processes. Cost-effective: Plate heat exchangers can offer cost savings compared to other types of heat exchangers due to their high heat transfer efficiency, and ease of maintenance. They require less space, materials, and installation costs, making them a cost-effective choice for many applications. Hygienic and Safe: Plate heat exchangers can be designed with sanitary features, including FDA-approved gaskets and stainless steel plates and components. Duo-Safety plates are also available which reduce the potential for cross-contamination between the product and the media..
A plate heat exchanger is a type of heat transfer device that is used to transfer heat between two fluids without them coming into direct contact. Plate heat exchangers are widely used in various industries and applications where efficient heat exchange is required. Some common uses of plate heat exchangers include: HVAC (Heating, Ventilation, and Air Conditioning): Plate heat exchangers are used in HVAC systems to transfer heat between hot and cold water streams for space heating, domestic hot water production, and cooling applications. They are commonly used in residential, commercial, and industrial buildings to efficiently heat or cool the air or water used for heating or cooling purposes. Industrial Processes: Plate heat exchangers are used in a wide range of industrial processes for heating or cooling fluids, such as oil, chemicals, gases, and other process fluids. They are used in industries such as chemical, petrochemical, pharmaceutical, food and beverage, pulp and paper, and many others for various heat exchange needs in processes like heat recovery, product cooling, condensing, evaporation, and pasteurization. Power Generation: Plate heat exchangers are used in power plants, including thermal power plants and nuclear power plants, for heat recovery from exhaust gases, cooling of lubricating oil, and other heat transfer applications. They help in improving the overall energy efficiency of power plants by utilizing waste heat for other purposes. Refrigeration: Plate heat exchangers are used in refrigeration systems for evaporators and condensers. They help transfer heat between refrigerant and the fluid being cooled, such as air or water, in order to achieve the desired cooling effect. Renewable Energy Systems: Plate heat exchangers are used in renewable energy systems, such as solar thermal systems and geothermal systems, for transferring heat between the renewable energy source and the working fluid. They help in capturing and utilizing renewable energy efficiently for heating or cooling purposes. Marine and Offshore Applications: Plate heat exchangers are used in marine and offshore applications for various heat transfer needs, such as engine cooling, oil cooling, and HVAC systems on ships, offshore platforms, and other marine vessels.
There are several types of plate heat exchangers, each with its own design and configuration to suit different heat transfer requirements. The most common types of plate heat exchangers include: Gasketed Plate Heat Exchangers (GPHE): These plate heat exchangers consist of multiple plates that are clamped together with gaskets to create separate channels for the two fluids. The gaskets provide sealing between the plates to prevent mixing of the fluids. Gasketed plate heat exchangers are versatile and can be easily disassembled for cleaning, maintenance, or plate replacement. They are commonly used for a wide range of applications with moderate to high-pressure and temperature requirements. Brazed Plate Heat Exchangers (BPHE): These plate heat exchangers are constructed by brazing the plates together using a filler material, which eliminates the need for gaskets. The brazing process creates a strong and leak-proof heat exchanger with excellent heat transfer performance. Brazed plate heat exchangers are compact and typically used in applications with lower to moderate pressure and temperature requirements. Welded Plate Heat Exchangers: These plate heat exchangers are welded together to form a robust and durable heat exchanger without any gaskets or filler materials. Welded plate heat exchangers are suitable for applications with high-pressure and temperature requirements and are commonly used in industries where corrosion resistance and mechanical strength are critical, such as oil and gas, chemical, and marine applications. Semi-Welded Plate Heat Exchangers: These plate heat exchangers combine both gasketed and welded designs, where some plates are gasketed and others are welded together. Semi-welded plate heat exchangers are used in applications where a combination of high-temperature and high-pressure requirements are needed, and the fluids being processed may contain particles or contaminants that can be easily cleaned or replaced on the gasketed side. Plate and Shell Heat Exchangers: These heat exchangers combine the design of a plate heat exchanger with a traditional shell-and-tube heat exchanger. They consist of a plate pack enclosed in a cylindrical shell. Plate and shell heat exchangers are used in applications where high pressure and temperature requirements are present, and they offer the advantages of compactness and ease of maintenance.